Industry 4.0 and Manufacturing: A Deep Dive into the Future of Production
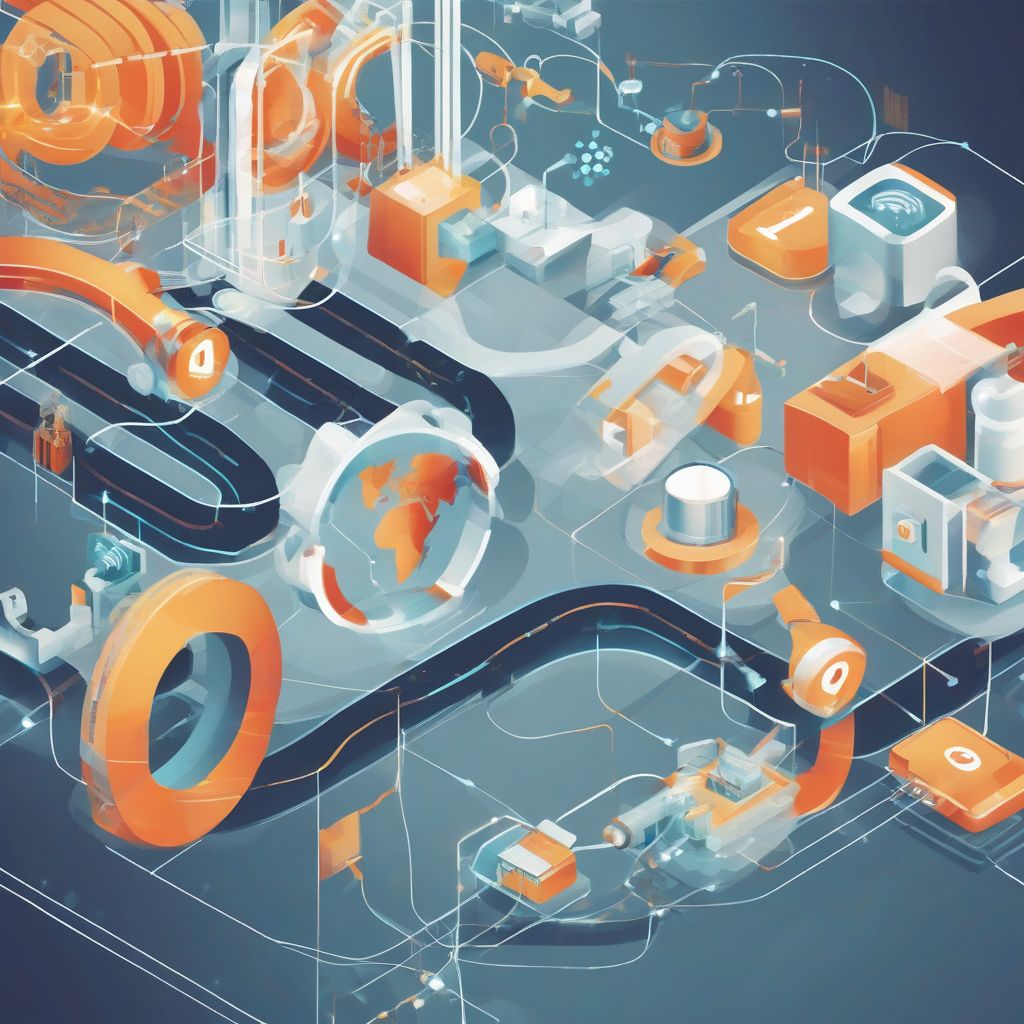
The manufacturing industry stands on the brink of a new era, driven by the powerful convergence of digital technologies and physical assets. This transformation, widely known as Industry 4.0, is reshaping the way things are made, from the factory floor to the global supply chain.
Industry 4.0 Concept Illustration
Understanding Industry 4.0 in Manufacturing
Industry 4.0 represents the fourth industrial revolution, building upon the previous revolutions marked by mechanization, mass production, and automation. This new era is characterized by the integration of cyber-physical systems, data analytics, and intelligent automation, creating a more efficient, flexible, and responsive manufacturing environment.
Here’s how Industry 4.0 is impacting manufacturing:
- Interconnectivity: Machines, systems, and people are interconnected through the Internet of Things (IoT), enabling real-time data exchange and collaboration.
- Data Analytics: Vast amounts of data collected from interconnected devices are analyzed to gain insights, optimize processes, and make informed decisions.
- Automation and Robotics: Advanced robotics, collaborative robots (cobots), and automated systems are transforming production lines, increasing efficiency and precision.
- Additive Manufacturing (3D Printing): 3D printing technologies allow manufacturers to create customized products, prototypes, and complex designs with greater flexibility.
- Cloud Computing: Cloud-based platforms provide access to computing power, storage, and software, enabling scalability and agility in manufacturing operations.
FAQs: Addressing Common Queries about Industry 4.0 in Manufacturing
As with any major technological shift, Industry 4.0 raises several questions and considerations for manufacturers. Here are some frequently asked questions:
1. What are the key benefits of adopting Industry 4.0 technologies?
Implementing Industry 4.0 solutions can lead to numerous benefits, including:
- Increased Efficiency and Productivity: Automation, optimized processes, and real-time data insights boost production output and reduce waste.
- Enhanced Flexibility and Agility: Manufacturers can quickly adapt to changing customer demands, produce customized products, and respond to market fluctuations.
- Improved Product Quality: Data analysis, automation, and advanced manufacturing techniques contribute to higher product quality and consistency.
- Reduced Costs: Increased efficiency, optimized resource utilization, and predictive maintenance lead to cost savings in the long run.
- New Revenue Streams: Industry 4.0 technologies enable the development of new products, services, and business models.
2. What are the main challenges in implementing Industry 4.0?
The transition to Industry 4.0 is not without its challenges. Some key hurdles include:
- High Initial Investment Costs: Implementing advanced technologies and infrastructure can require significant upfront investment.
- Data Security Concerns: The interconnected nature of Industry 4.0 raises concerns about data security and privacy.
- Skills Gap: A workforce skilled in digital technologies, data analytics, and automation is crucial for successful implementation.
- Legacy System Integration: Integrating new technologies with existing legacy systems can be complex and require careful planning.
3. How can companies prepare for the Industry 4.0 revolution?
- Develop a Digital Transformation Strategy: Outline a clear roadmap for adopting Industry 4.0 technologies aligned with business goals.
- Invest in Workforce Training and Development: Upskill and reskill employees to bridge the digital skills gap.
- Foster a Culture of Innovation: Encourage experimentation, collaboration, and continuous improvement to embrace new technologies and processes.
- Partner with Technology Providers: Collaborate with technology companies and industry experts to leverage their expertise and solutions.
Industry 4.0 in Action: Real-World Examples
Numerous companies across various sectors are already reaping the benefits of Industry 4.0 implementation. Here are a few compelling examples:
- Siemens: The German industrial giant utilizes a digital twin of its Amberg factory, allowing for virtual simulations, optimization, and remote monitoring, resulting in a 99.99885% quality rate.
- Bosch: The global supplier of technology and services employs connected tools and data analytics to optimize production processes, improve product quality, and predict maintenance needs.
- GE Aviation: By leveraging additive manufacturing, GE Aviation is producing lighter and more fuel-efficient jet engine components, revolutionizing aircraft design and performance.
The Future of Manufacturing is Here
Industry 4.0 is not merely a technological evolution; it’s a fundamental shift in how manufacturing operates. As technologies continue to advance, we can anticipate even greater levels of automation, intelligence, and interconnectivity. Companies that embrace this transformation will be well-positioned to thrive in the increasingly competitive and dynamic global marketplace.
Leave a Comment